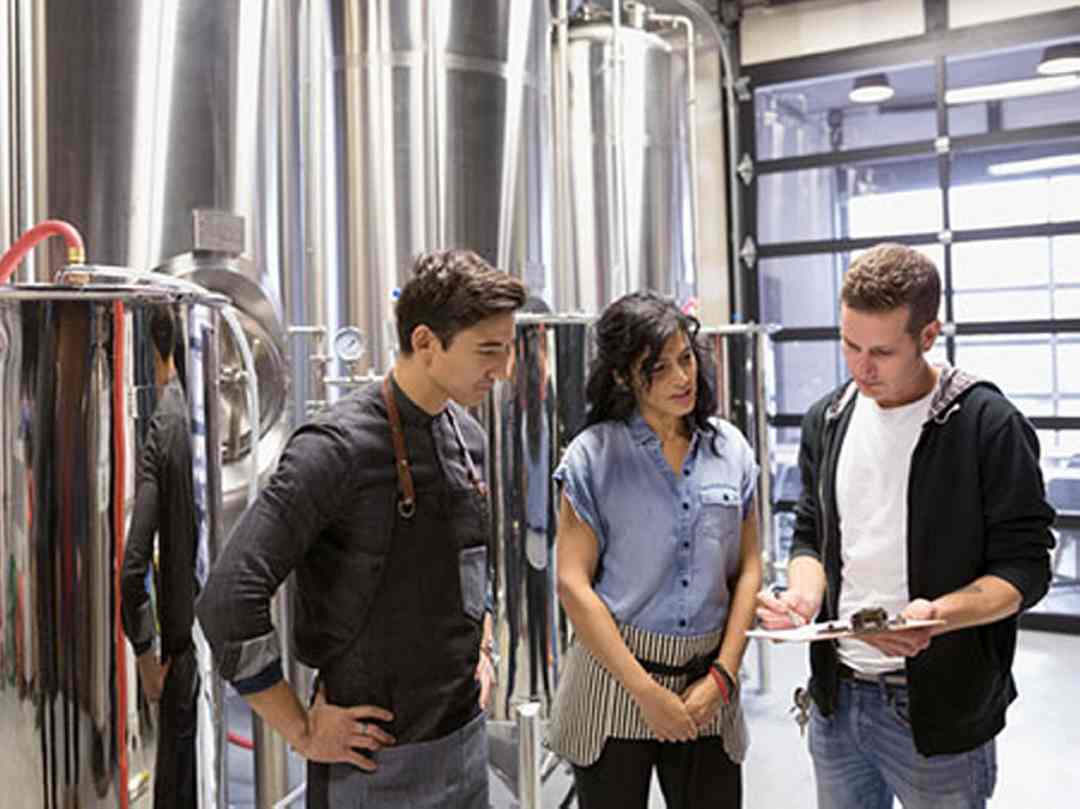
Actions to maintain the brewery ‘household’ secure
Companies need to take actions to assist maintain brewery employees secure.
With ever-evolving beer designs, breweries, taprooms and also beer yards, it’s been enjoyable to participate in the craft brewery transformation. When you witness the friendship, it ends up being clear that several breweries resemble a family members. Workers aspire to invest several hrs with each other establishing brand-new dishes, burning the midnight oil to satisfy the following day’s orders and also establishing performances to stay up to date with boosting need.
Together with the development and also exhilaration comes the demand for security and also threat monitoring. Nobody wishes to see a member of the family experience a significant injury, so it makes good sense to check out some dangers staff members encounter at the brewery each day.
Below is a recap of 4 of the leading offenses of Occupational Health and wellness Management criteria that impact the sector, with a quick summary of what a company can do to handle each risk.
Risk Interaction– 1910.1200— Workers have a right to understand about the harmful chemicals they are subjected to in the developing procedure, consisting of caustics and also acids utilized in hygiene of the developing procedure. They need to get security training on correct individual safety tools (PPE) and also emergency treatment reaction. They additionally need to have accessibility to all Security Information Sheets for harmful chemicals. Given chemicals kept in containers such as spray containers go through added labeling needs.
Shut Out Tag Out– 1910.147— This typical addresses the methods and also treatments for disabling equipment or tools to stop the launch of harmful power throughout upkeep or maintenance. Dangerous power can consist of electric, mechanical, hydraulic and also pneumatically-driven. Needs consist of having actually a recorded program, performing staff member training and also recognizing the details tools covered by this requirement. Devices in a brewery can consist of milling tools, pumps, agitators, canning, bottling and also product packaging tools.
Restricted Area Entrance– 1910.146— Aspects of this typical secures staff members operating in restricted rooms, which are specified as an area with restricted or limited access and also departure and also not planned for continual tenancy. A license access procedure is called for when the location has dangers of hazardous environment; capacity for being swallowed up, entrapment or asphyxiation; or any kind of various other acknowledged major risk that might threaten the security or health and wellness of a worker. Containers and also fermenters utilized for developing can consist of one or numerous of these dangers such as oxygen shortage, mechanical agitators, warm surface areas and also heavy steam. Amongst the needs, companies have to:
- specify the restricted rooms
- assign those calling for allowed access
- produce a certain treatment to separate the risk related to the area
- train staff members
- produce a procedure to get in the area with security controls for shutting out power and also risk resources
- offer PPE for staff members
- conduct tracking, rescue and also emergency situation reaction
Powered Industrial Trucks– 1910. 178— Breweries utilize forklifts and also various other mobile tools to relocate hefty tons, totes, pallets of items and also basic material. All drivers have to be educated on the tools they’ll utilize by a certified individual with required experience and also expertise of the details tools. Training needs to be given before running the tools and also consist of class, abilities and also driver expertise. Driver efficiency need to be recorded every 3 years, and also re-training is called for complying with any kind of proof of inadequate efficiency, near miss out on or mishap or if problems alter.
These are just a couple of of the OSHA criteria that relate to dangers that makers and also their staff members encounter daily in their procedures. The Occupational Security and also Health and wellness Act itself needs companies to offer a risk-free workplace devoid of acknowledged dangers and also checklists added needs for document- maintaining and also yearly injury and also health problem posts. The full checklist of OSHA offenses for this sector can be discovered right here.
This loss control info is advising just. The writer presumes no duty for monitoring or control of loss control tasks. Not all direct exposures are recognized in this short article. Get in touch with your regional, independent insurance coverage representative for insurance coverage recommendations and also loss control solutions.